PALLADIUM-COATED METAL MEMBRANES FOR ULTRA HIGH PURITY HYDROGEN AND FUTURE APPLICATIONS
Robert E. Buxbaum
REB Research & Consulting, 12851 Capital St, Ferndale, MI, 248-545-0155.
Ultrapure hydrogen is used throughout industry, for example in the manufacture of semiconductors, for silicon epitaxi, and as a carrier gas for dopants. These applications allow no more than 100 ppb impurities in the hydrogen, and purity limits are expected to tighten as manufacturers go to increased transistor densities over the next decade. Currently, ultrapure hydrogen is supplied either as a bottled gas, or as a liquid whose boil-off causes pollution and safety concerns, and whose boiling pressure, 90 psig, limits the maximum operating pressure where liquid hydrogen is used. In either case, the hydrogen arrives with 10-100 ppm impurities and must be further purified to 100 ppb, typically by use of palladium-membranes. The last 100 ppb are mostly methane from carbon that permeates through the palladium silver at the operating temperatures of ~ 400 C and from degassing of the steels used in module construction. The technology could produce purer hydrogen by operating at lower temperatures, but practical considerations limit purity to about 10 ppb because the hydrogen flux through the membranes falls off. Going to 300 C operating temperatures increases the purity by 50 x, but requires more than 5 times as much membrane as when operating at 400 C. Projected ppt purities can be reached only at great cost with palladium silver. For these needs, we have developed a membrane that operates with high flux at much lower temperatures 275 C and below.
Figure 1 shows the permeation of hydrogen through several metals as a function of temperature. Hydrogen permeability through palladium is fairly high at 700 C, but decreases sharply with decreasing temperature. Several other metals, including vanadium, niobium, and tantalum have much higher permeabilities at these lower temperatures. The metals themselves are poor choices because they embrittle too badly at room temperature in the presence of 100 psig hydrogen, but several alloys of these metals are also non embrittling, making them good candidates for hydrogen purification membranes. For a similar size membrane the flux can be ten times higher than with palladium silver, at the target temperatures of 300 C and below.
The refractory metals have several other advantages over palladium as well. They are much cheaper per unit volume and have much greater high temperature strength. These metals are not normally used for hydrogen permeation because of poor surface properties, particularly surface oxide layers, that slow the hydrogen transport. When palladium or palladium alloys are applied over the surface of refractory alloys the surface barriers are removed and hydrogen permeation approach levels shown in figure 1. Several groups have described or patented aspects of this technology to the point where it is now commercially availably for small applications. Patents and interesting papers include Makrides et al. at Harvard University (1) , this author at REB Research & Consulting (2,3), Darling at Johnson Matthey (4), Edlund et al at Bend Research (5) Amano et al in Japan (6), Hill at Argonne West (9), and Peachey et al at Los Alamos (10). Figure 2 shows a picture of this author with several membrane modules made to support this technology. The smallest of these modules purifies about 8 l/min at 300 C.
Figure 2: Author with several modules
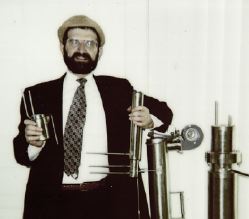
Theory
Since hydrogen molecules dissociate into atoms to diffuse through a metal membrane, transport is calculated from the atomic flux. For a homogeneous layer
NH = -D M ( CH/dM ) (1)
where NH is the atomic flux, D M is diffusivity, CH is the change in hydrogen atom concentration across the layer, and dM is the layer thickness. CH is related to the partial pressure of hydrogen in equilibrium with the metal:
CH = K S (P1/2) (2)
where K S, is the Sieverts constant, and P is the partial pressure of hydrogen in equilibrium with the metal. The power of 1/2 comes from the dissociation of hydrogen molecules into twice as many atoms at low concentration. We now calculate the flux of hydrogen molecules, N, in terms of pressure using equations 1 and 2. The flux of molecules is half the flux of atoms:
N = (D M K S/2 dM ) P1/2 = P M P1/2/dM . (3)
The term P M = D M K S/2, above is called the metal permeability, a pressure-independent constant for a given metal at low hydrogen contents. The 'total resistance to transport' is defined as:
R Tot = P1/2/ N = d/P . (4)
In a layered membrane this total transport resistance, R Tot, is the sum of the resistance in each layer ( dM/P M ) plus the effective resistance of surfaces and gas diffusion.
Permeabilities of the refractory metals vanadium, tantalum, zirconium and niobium are so large that until recently they were inferred only from diffusivity and low concentration solubility coefficients (7). Recent measurements have confirmed that these metals are significantly more permeable than palladium when coated with palladium (8,9,10).
Permeability and Durability Measurement
Our experiments use tubular membranes rather than discs because tubes allow a thinner wall for a given pressure differential, and thus allow higher hydrogen fluxes. Also, tubular membranes are easier to scale up, eg. using a shell-and-tube heat exchanger design. Most of our recent experiments use low embrittlement alloys because these are thought to have more commercial potential. We draw these alloys into tubes with wall thicknesses as small as 0.007 cm, and lengths up to 8'. We cleaned these tubes and applied palladium as previously (3), but used hydrazine as the reducing agent instead of hypophosphate. Where possible, the tubes are coiled and sealed either with swagelok or braze seals. To measure permeation, impure hydrogen-gas, or a mixture of hydrogen and CO (a model for reformate off gas), is heated to operation temperature, and then flowed past the membrane. Much of the hydrogen permeates the membrane and the rest exits along with the impurities. We measure the flow of hydrogen through the membrane and the gas pressures at the inlet and exits. We then calculate a per area flow as shown in Fig 3. We regularly check for leaks by analyzing the output hydrogen purity.
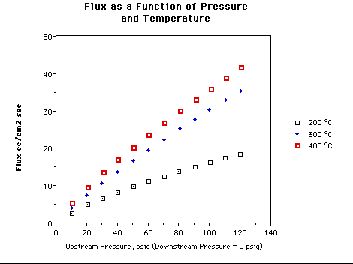
Figure 3 shows some flux data with a coated REB Research membrane. At 300 C and a pressure differential of 80 psig, this flux is.3.5 times higher than the flux of the best palladium-silver membranes at this critical temperature and pressure differential; 80 psi represents the difference between 90 psig upstream for liquid hydrogen boil-off sources and 10 psig downstream. We produce more-or-less the same flux data for several different substrate membranes. Apparently, many membrane substrates give order of magnitude improvement over palladium silver. The average membrane permeabilities of V-Ti based membranes is 0.15 moles m/m2sPa0.5 at 600 C and 0.015 moles m/m2sPa0.5 at 300 C; for V-Nb membranes, the permeabilities are 0.2 moles m/m2sPa0.5 at 429 C and 0.19 moles m/m2sPa0.5 at 340 C. Substrate optimization may depends on application, pressure and temperature, and may ultimately depend on drawability or brazeability. Currently the cost to draw tubes and the cost of sealing the membranes into modules is higher than the materials cost for all modules tested.
Hydrogen impurity levels are below the detectable limit at these temperatures.
Automotive and chemical applications
Two long-term applications for these membranes are hydrogen-powered automobiles, and chemical plant use. The most likely engine for hydrogen powered automobiles is the polymer-electrode fuel cell, as made, e.g. by Ballard of Canada. These fuel cells are over 40% efficient vs 20% for standard gasoline engines and achieve further energy advantages when regenerative braking is added. Further, since they work at low temperatures they start up without a long warm-up period as with other fuel cells carbonate, phosphate, etc. But practical automobiles also need a practical fuel source and a low temperature hydrogen ultrapurifier. Methanol reformation is one practical fuel source but it currently is pared with palladium-silver membrane purifiers operating at 350 C, and these require a long warm-up. If our technology can be extended to room temperature operation, we will have a truly practical fuel-cell car, but we are not there yet. REB Research has built and begun to test an experimental, Mr. Hydrogen membrane reactor that produces hydrogen from methanol at 250 C. It has run for several weeks without problem, but will need to run longer and cooler to be commercial.
Our metals' permeabilities are about 20,000 times higher than equivalently thick polymeric membranes, but they are still not competitive for most chemical-plant hydrogen extractions. Our membranes are typically much thicker than polymer membranes (75 vs 0.1 thick) and cost more, about 1000/ft2 vs $10/ft2. If we can decrease the tube wall thickness or increase the flux by an order of magnitude though, the cost/flux ratio will favor metallic membranes, even where high temperature operation and ultra-high purity are not needed.
We gratefully acknowledge financial support from the Department of Energy under Phase 1 and 2 SBIR grants, Numbered DE-FG02-93ER81625.
References
(1) A.C. Makrides, M.A. Wright, and D.N. Jewett, "Separation of Hydrogen by Permeation," U.S. Patent, 3,350,846, Nov. 7, 1967.(2) R.E. Buxbaum, "Composite Metal Membranes for Hydrogen Extraction," U.S. patent 5,108,724, December 15, 1991.
(3) R.E. Buxbaum and P.C. Hsu, "Method for Plating Palladium," U.S. patent 5,149,420, issued September 22, 1992.
(4) D. Edlund, "Metal Membranes for High Temperature Gas Separations," Proc. the 1990 Membrane Conference (Business Communications, Norwalk, Conn., 1991) p. 77.
(5) A.S. Darling, Johnson Matthey, "Improvements in or Relating to the Separation of Hydrogen from Gaseous Mixtures containing Hydrogen" British Patent 1,292,025, published 11 Oct. 1972.
(6) M. Amano, M. Komaski and C. Nishimura, "Hydrogen Permeation Characteristics of Palladium Plated V-Ni Alloy Membranes, J. Less Com. Met. 172-174 (1991) 727-731.
(7) S.A. Steward, "Review of Hydrogen Isotope Permeability through Materials," Lawrence Livermore National Laboratory Report, UCRL-53441 (1983).
(8) R.E. Buxbaum and A.B. Kinney, "Hydrogen Transport through Tubular Membranes of Palladium-Coated Tantalum and Niobium, I&EC Research 35 (1996)530-537.
(9) E.F. Hill, "Feasibility Study: Removal of Tritium from Sodium During the MDEC Process by Oxidative Diffusion", Argonne West, DOE N707T1830035 (1982).
(10) N.M. Peachey, R.C. Snow, and R.C. Dye, "Composite Pd/Ta Membranes for Hydrogen
Separation," J. Membrane Sci., Vol. 111, p. 123 (1996). copyright 2010